Picking efectuádo con pick to box
El SGA ( Sistema Gestión Almacenes ) SACA fué pionero en introducir el procedimiento de pick to box para la preparación de pedidos. Esta solución, óptima bajo puntos de vista de eficacia y rentabilidad en zonas de picking de media y baja rotación, permite la preparación simultánea de varios pedidos sin necesidad de posteriores repartos.
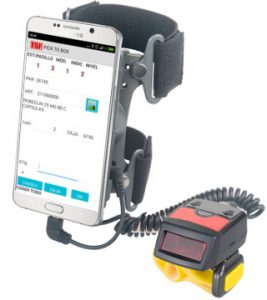
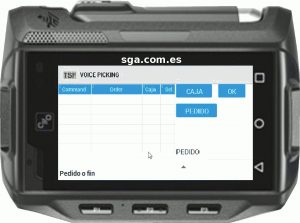
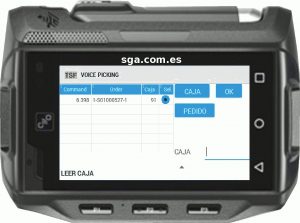
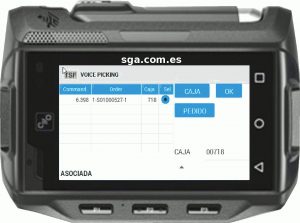
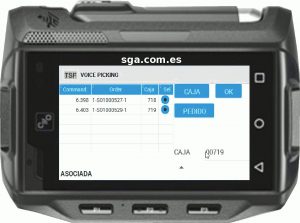
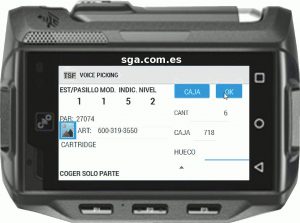
Cuando comienza un ciclo de reparto, el operario selecciona pedidos y asigna a cada uno una caja o gaveta de recogida. A medida que el SGA le va indicando el material a recoger, también le indica la caja o gaveta en qué depositarlo, permitiendo así llegar al final del recorrido de recogida en su zona de trabajo con el material recogido y depositado en sus cajas correspondientes. Esta forma de trabajo disminuye notáblemente los recorridos entre puntos de recogida de material con relación a la recogida de pedidos uno a uno, aumentando así en gran manera la productividad de los operarios en la recogida de pedidos con una inversión fácilmente recuperable.
Esta operativa se complementa con la posibilidad que proporciona el SGA SACA para mejorar el pick to box de segmentar el almacén en diversas zonas de recogida, lo que permite tanto modular el número de pedidos cuyo servicio se realiza agrupado, para así usar mayores cajas o gavetas en las zonas de artículos de mayor rotación o mayor volumetría, como tener recorridos más cortos para evitar que se llenen las cajas o contenedores en medio de una zona de recogida. Al final de una zona de recogida y comienzo de la siguiente, las cajas llenas son enviadas directamente a la zona de expediciones y sustituídas por nuevas cajas asociadas a sus pedidos, y se continúa la recogida sobre las cajas a medio llenar y sobre las nuevas.
Una solución que puede complementar el pick to box es el uso de carritos de picking equipados con pick to light. Podemos ofrecer tanto el diseño y la fabricación de dichos carritos, como el equipamiento electrónico necesario para transformar carros de recgida existentes así como todo el software e infraestructura de comunicaciones necesarios para su operativa.
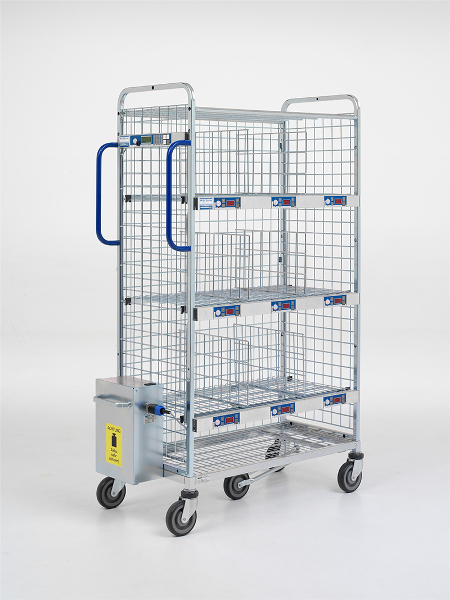
En los carritos de recogida los visores pick to light están normalmente dispuestos en hileras colocadas en la parte frontal de las bandejas de los carritos. En cada frontal de cada posición de pedido está situado un visor, y todos ellos están unidos en una arquitectura de bus serie multipunto bajo norma RS285 a un concentrador/convertidor de normas, conectado al sistema de gestión de los módulos vía red ethernet con protocolos TCP/IP. Este controlador se conecta a la red general a través de un cliente
WiFi. La alimentación se efectua directamente a 12 V a través de un estabilizador y un sistema de baterías
En el funcionamiento habitual de este tipo de sistemas, se extraen los artículos a repartir mediante el control del SGA, que extrae asociadas las cantidades de cada artículo correspondientes al lote de pedidos en servicio. Cuando comienza un ciclo de reparto, el sistema asigna a cada posición del carrito un pedido. Mediante unos visores principales, el sistema le muestra al operario el código del artículo a recoger y su ubicación. Cuando el operario recoge el material, lee el código de barras del producto o de su ubicación con un escáner de lectura conectado al carrito y el sistema muestra en los visores correspondientes las cantidades a colocar en cada gaveta, enviándoselas a través de la red WiFi. El operario las va colocando y pulsando los botones de confirmación, con lo que se van apagando los visores de los pedidos ya servidos, este hecho generará los correspondientes mensajes, que serán recogidos por la rutina del SGA, que confirmará así el reparto del producto y permitirá avanzar en la secuencia de recogida de productos. En el caso de discrepancias en la recogida estas se harán constar mediante dos pulsadores de incremento/decremento de la cantidad servida.